ProDog
The ProDog (End Dogger System) is a complete primary breakdown solution that offers piece counts and gaps comparable to sharp-chain-style systems. Full rotation of logs gives the highest recovery possible. Our dual carriage ProDog system provides canting, double profiling, and a quad saw box in only 8.5’. As with all our HOTT Technology systems, all critical components are located above the cutting tools and debris.
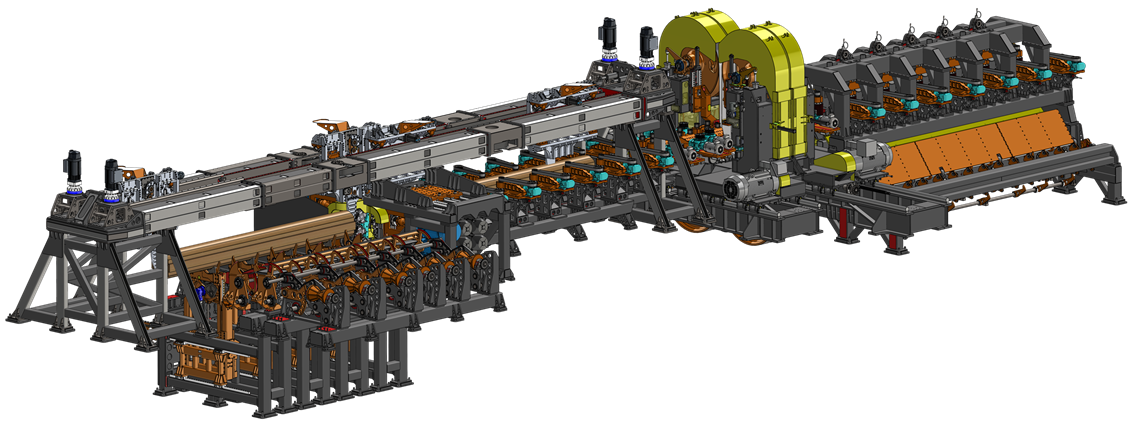
Charging System
- Scanning done upstream giving optimizer 2-4 seconds of solution time
- Logs come in with consistent log line
- Charging yokes and infeed equipment controlled by electric servo
- Optimized pre-rotation is done in turner arm before final positioning and rotation offsets are completed
- Final positioning and rotation offsets are calculated by the scanner while the log is clamped in the same mechanism that executes the offsets
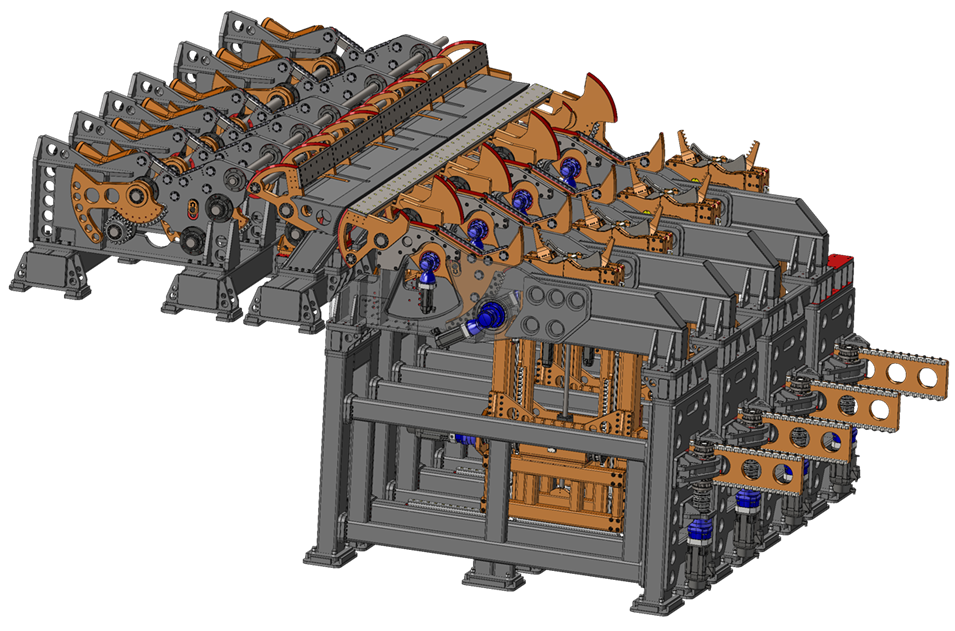
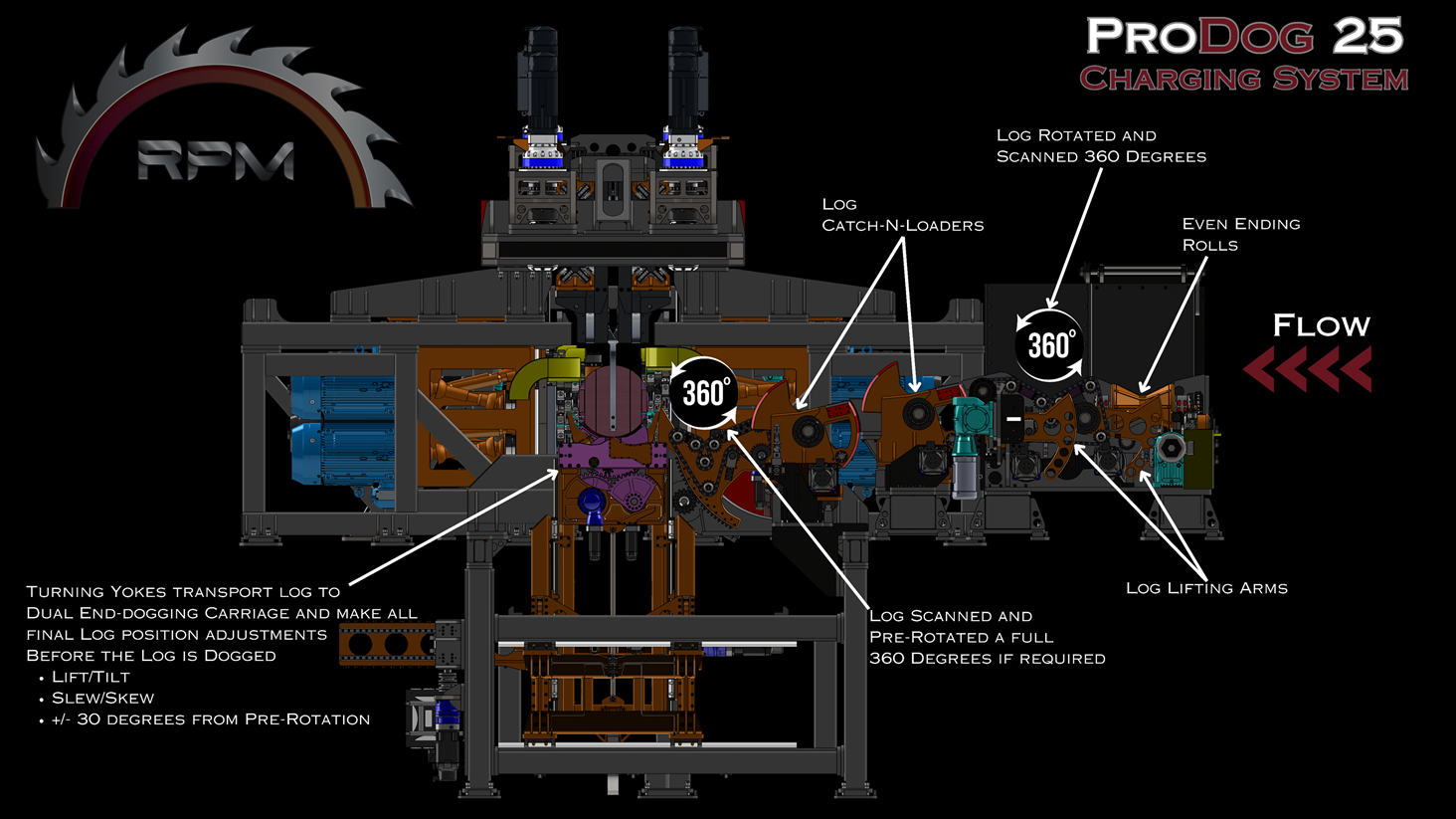
- All Electric X-Y Turning Yokes
- Turning yokes can rotate logs an additional +/- 30 degrees for final correction after optimized pre-rotation
- Zero backlash roller pinion actuates yokes in/out
- Zero backlash roller pinion actuates yokes up/down
- Dual servo motors work together to clamp and rotate logs with minimal following error
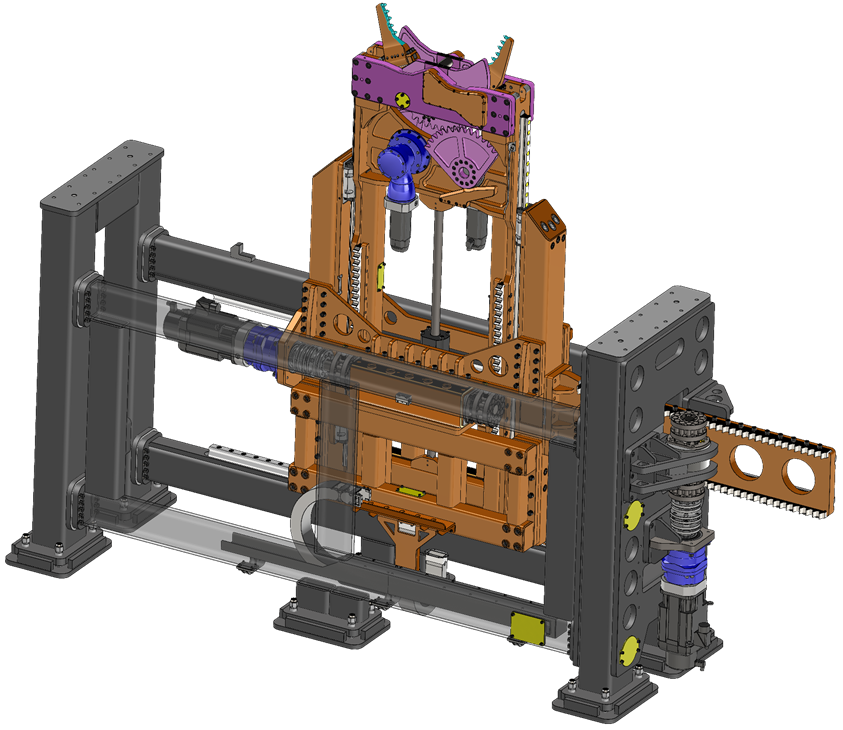
Charging System - Start-Up
- Startup video shows slower than production speed
- Final scan of the log is done after the log is clamped
- Final rotation and positioning (slew, skew, left, tilt) are done with the log clamped exactly how it was scanned
- Scanning done offline; positioning done as the log moves to centerline
- No rolls attempt to rotate and position unpredictable log surfaces
- Short overall footprint compared to sharp-chain-style system
- No rotation limitations due to log instability on a sharp chain
- Typical 3% increase in recovery due to log positioning accuracy
Charging System - Production
- Production Video
- This system runs 20 - 22 LPM (logs per minute)
- Logs come in with a consistent lumber line
- This shows a single scan zone with geometric turners that use gravity to get the log horns up/down
- Lower piece count systems can use the scanner to pre-scan and pre-rotate in the turner arm
- Higher piece count systems can utilize a second scan zone to achieve the same full 360-degree rotation solutions
Carriages
- Carriages constructed out of 3", 2.5", and 1.5" thick 7075-T6 Aluminum (higher strength than A36 steel at one-third of the weight)
- Carriages ride on Thomson Roller RoundWay bearings for high speed and long life
- Carriages are driven by an oversized 150mm wide timing belt with higher load ratings than conventional cables
- Dog arm utilizes over-center cam geometry to lock the dog arm in the down position
- All-electric actuation of carriage travel and dog arm lift/lower
- Replaceable break-away dog arm
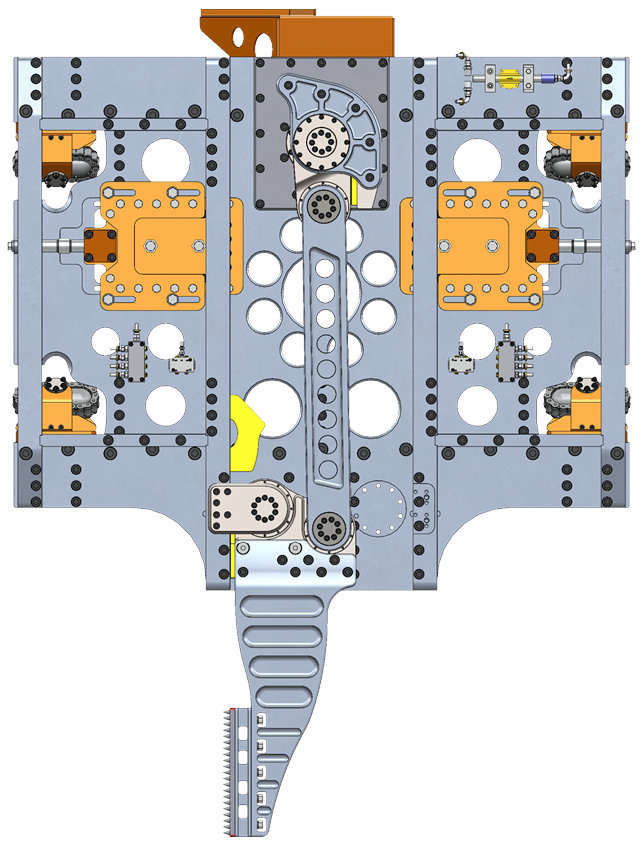
Carriage Drives
- Carriage drives use 150mm wide timing belts on edge for tight packaging and debris management
- Carriages have two clamping points that the belts attach to
- Each carriage is driven by a large servo motor and gearbox with low backlash (3 arc min or less)
- Drive configuration uses large spherical roller bearings with common parts between head and tail
- Belt tensioning is done at carriage to allow head and tail to stay fixed
- Belts are a Polychain style with 20mm pitch, up from the common 14mm
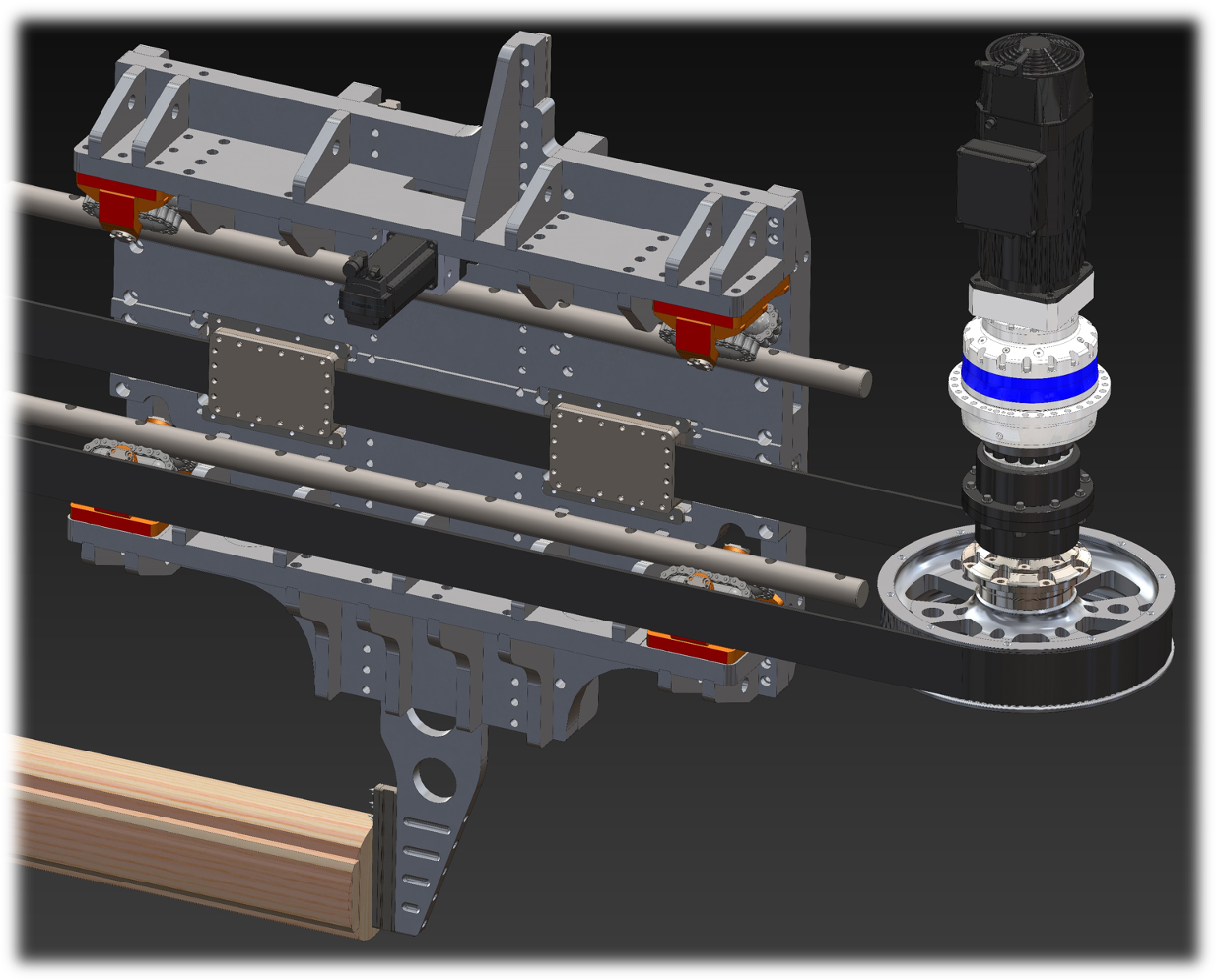
Carriage Beams
- Beams constructed of double-stacked 8” by 10” by 1/2” HSS Tube and 3” solid steel plate
- Precision machined in one setup after fabrication
- Top and Bottom Thomson RoundWays bolt to a single 3” vertical plate
- Timing belts run inside the beam structure, kept out of harms way
- Belt access points are intermittently cut into the beam structure
- Support structure is made from 6” by 10” by 1/2” HSS tube and heavy plate
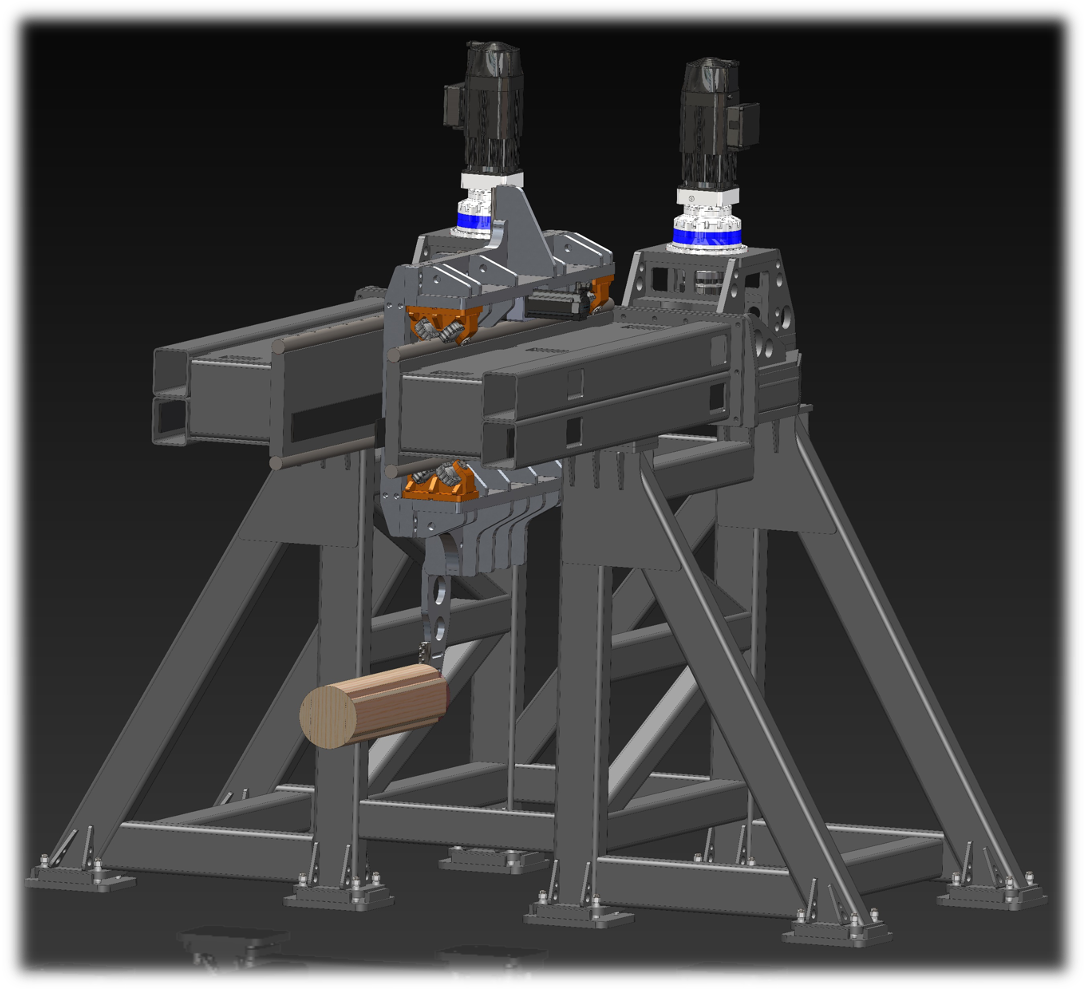
Cutting Tool Flow
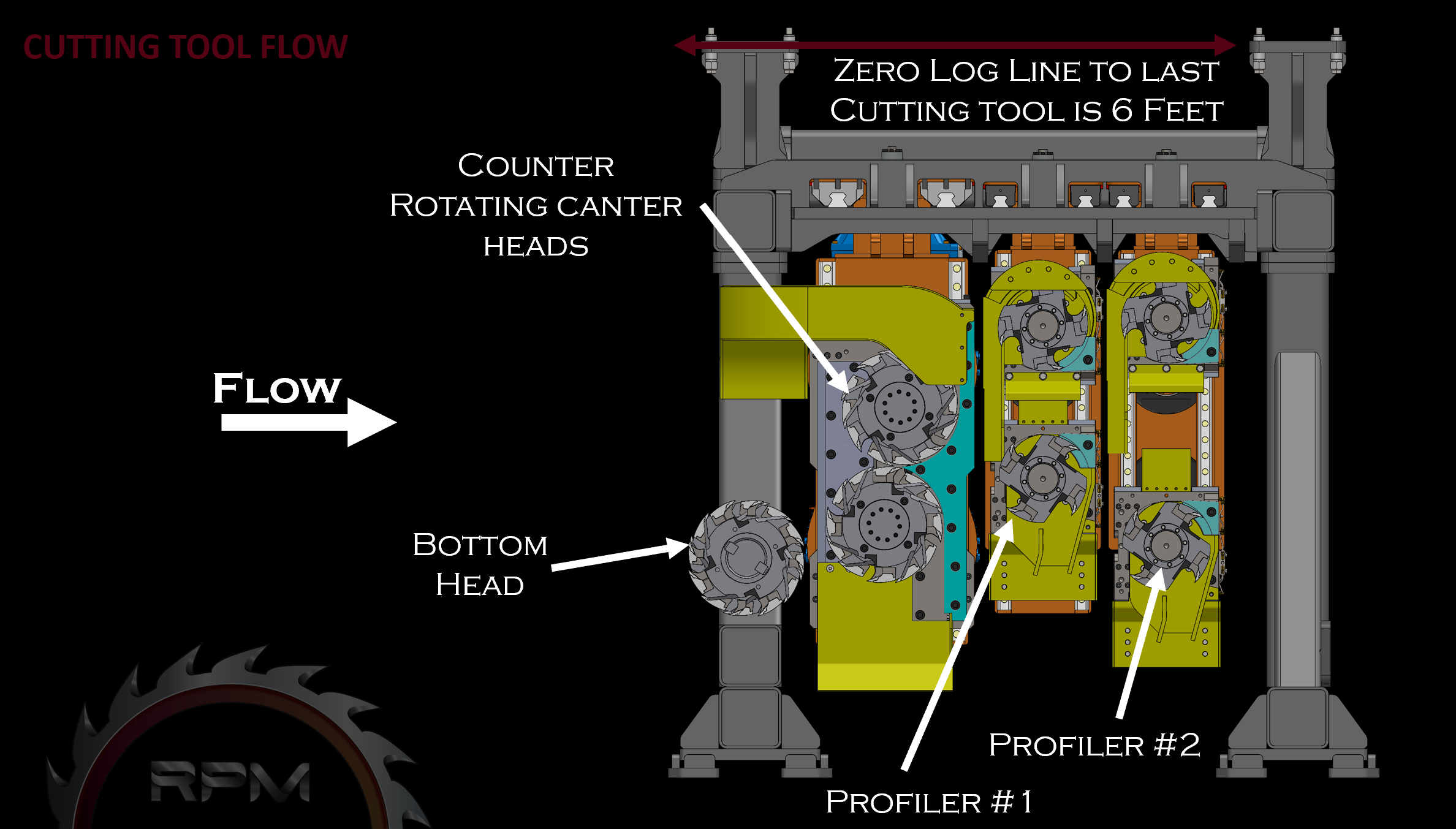
Canter Profiler Module
- Module constructed of 3”, 2”, and 1.5” A36 steel plate
- Main carriage rides on 65mm INA linear bearings
- Canter heads counter-rotate for equal chipping force
- All top cutting tools are driven by one motor
- All bottom cutting tools are driven by one motor
- All cutting tools are driveline driven for simplicity
- All cutting tools use proven and common spindle assemblies
- Profiler tools are independently positioned for slewed sideboard solutions
Double Arbor Quad Sawbox
- There are two movable saw boxes that move instead of the conventional fixed arbor moving guides configuration
- This allows for a much more rigid arbor and guide design to achieve higher sawing speeds while increasing accuracy
- Single motor for each side of the machine
- Top arbor offset automatically adjusted to eliminate saw mismatch
- Arbors can be configured as a twin or quad depending on the installed guide arrangement
- 24” Diameter Saws with a .150” Kerf sawing Southern Yellow Pine
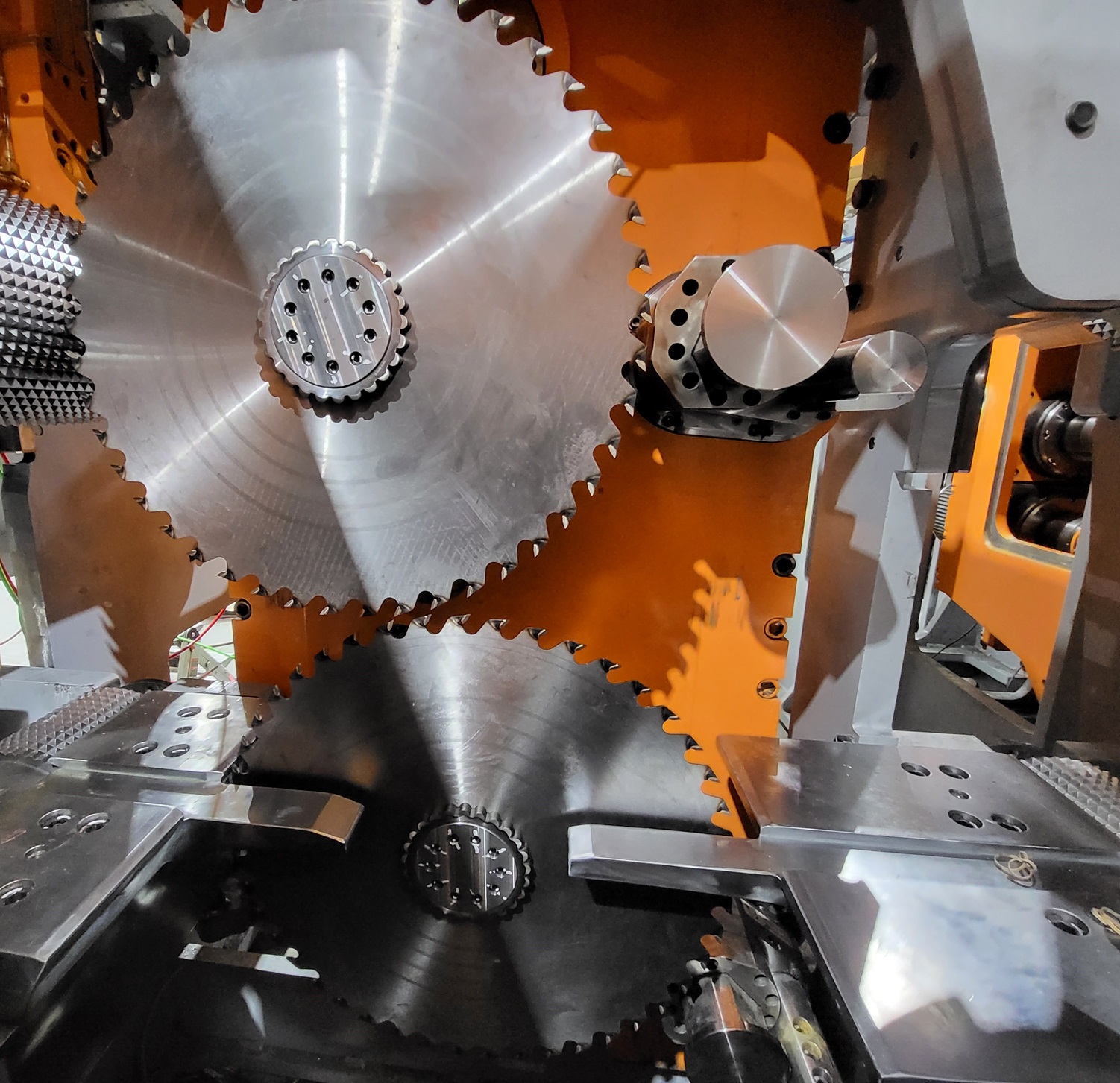
5-Way Outfeed Dispatch
- Outfeed can separate to five different downstream locations
- Inertia separators below the feedline divert boards/flitches to the desired location (Backline, Re-saw, Board Edger, etc.)
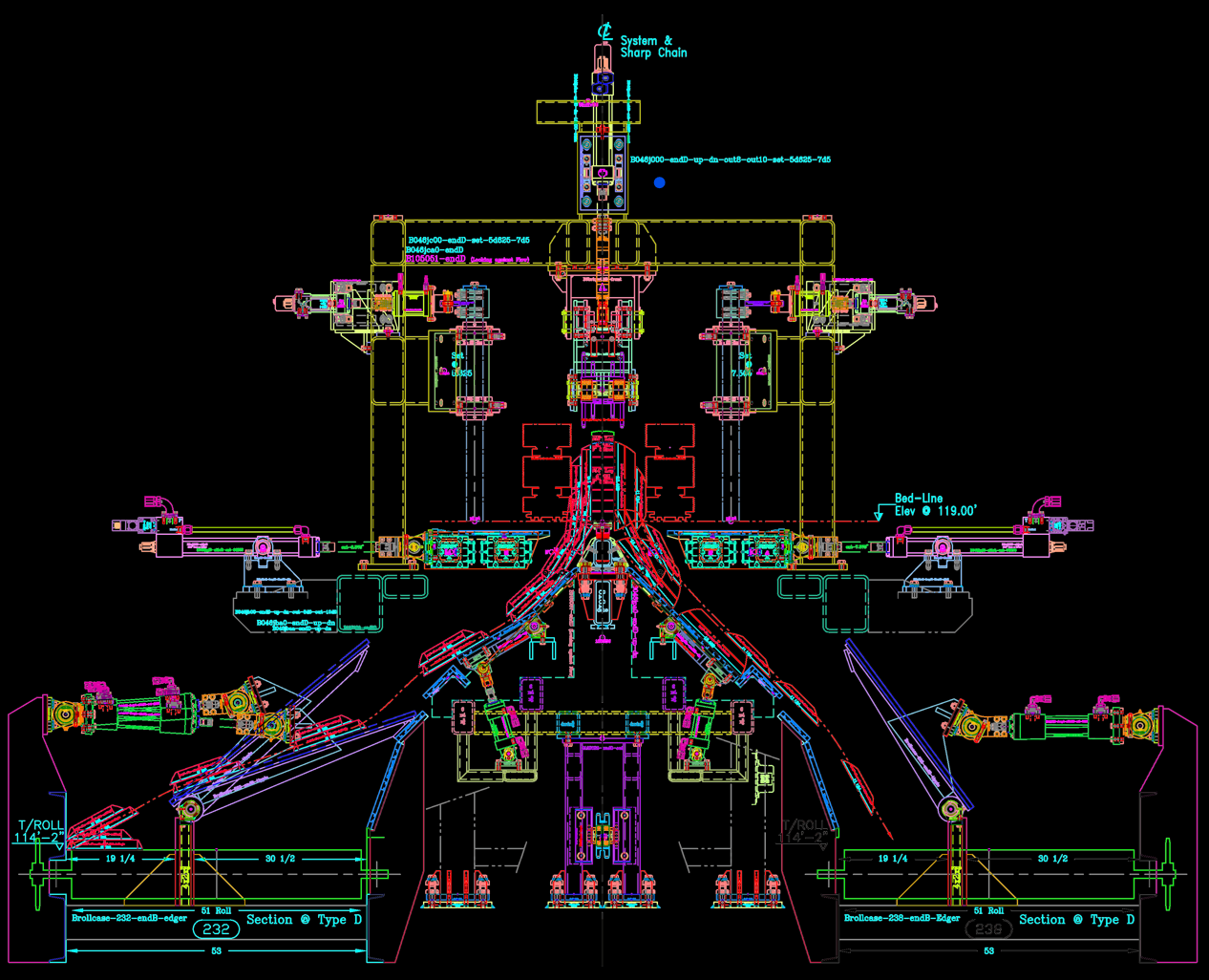